Selecting the Right Materials and Construction Techniques for Process Plant Steel Structures
Discover the art of designing process plant steel structures, where safety, efficiency, and durability take center stage. With meticulous attention to detail and a deep understanding of engineering principles, our experts ensure that every structure is meticulously crafted to safeguard individuals and assets. Lean into our expertise and unlock the potential for efficient processes, seamless operations, and long-lasting durability in your industrial facility.
Phase 0 – Establishing the Design Basis
In the design of steel structures, several factors need to be taken into consideration. This includes applicable codes, company specifications, and standards that must be followed. Additionally, the type of steel profiles to be used will vary based on their sourcing location, such as Europe, US, China, Japan. Design criteria like maximum allowable stress ratio and deflection should also be considered. The basis for applying loads and the type of fixing structures on foundations (rigid or pinned) are important elements in the overall design process. A crucial document in the realm of structural design is the “Structural Design Basis.” This comprehensive guide serves as a valuable resource for structural engineers, offering them guidance throughout the project execution life cycle. Its purpose extends beyond just providing instructions; it also acts as a reliable reference document that ensures consistency and accuracy in project implementation.
Phase 1 – Designing the Primary Structure
To begin the steel structure design process, the focus is on crafting a robust main frame for the structure. This primary structure comprises essential components such as columns, main beams, and bracings. These elements form the backbone of the design, ensuring stability and strength throughout the entire structure.
At this point, the input data consists of the overall structure’s geometry and the process loads, which include equipment and main lines.
The geometry of a structure is established through the Layout discipline, which involves creating a preliminary model within the Plant 3D model, such as SmartPlant or PDMS. This entails not only considering the space taken up by equipment, but also their surroundings (instruments, piping, valves), as well as access platforms and ways required for operational and maintenance purposes.
Once you have developed your preliminary model, it can easily be imported into the widely used 3D Modeling Software’s software for steel structure detailing. This seamless integration enables a smooth workflow and ensures accurate and efficient design execution. Utilizing 3D Modeling Softwares will definitely enhance the overall efficiency of your steel structure detailing process.
When it comes to equipment data, it’s crucial to have accurate information on the empty and operating weights of each piece of equipment. However, in situations where vendor information is not immediately available, it becomes necessary to make estimations based on similar equipment or jobs. By taking a conservative approach and relying on analogy equipment or jobs, you can ensure that your estimates are as reliable as possible.
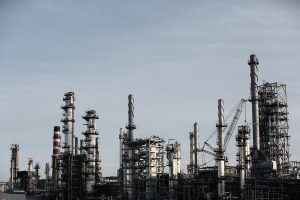
When it comes to lines, individual loads may not be taken into account, except for a few instances where there are large and heavy lines [1]. However, the loads from other lines are factored in using a loading factor. For example, the pipe rack beam might have a loading factor of so many kN/m, while the process structure floor may have a loading factor of so many kN/m2. This approach ensures that all relevant load considerations are properly addressed.
When it comes to handling horizontal loads caused by thermal expansion in lines, it’s important to focus specifically on the loads impacting the supports of the lines entering or leaving the structure. These are the ones that have a direct influence on the primary structure, while any other loads remain internal and don’t impact its overall integrity.
In addition to the aforementioned factors, it is crucial to take into account other significant loads such as pipe supports, floors (grating and plating), Passive Fire Protection, E&I items, handling requirements, potential ice/snow loads, and blast considerations if applicable. Ensuring all these elements are carefully considered guarantees a thorough assessment for optimal performance and safety.
When it comes to modular structures transported as blocks, careful consideration must be given to the lifting and transport process. In addition to the “in place” analysis, additional calculations are necessary. Temporary structural members should be included in order to accurately account for the specific load cases related to these operations. This ensures a safe and successful transportation of the modular structures while maintaining their integrity.
Design and modelling software
To ensure the utmost precision and efficiency in designing the main structure, professionals rely on dedicated software such as STAAD. Pro. This powerful tool allows for the detailed definition and optimization of structural steel members, as well as accurate positioning of bracings. With its widespread use in the industry, STAAD. Pro has proven to be an invaluable asset for engineers and designers alike.
Structural design plays a crucial role in ensuring the stability, strength, and rigidity of buildings. It involves analyzing every structural element and considering the structure as a whole. The primary goal of structural design is to create a robust structure that can withstand various loads, such as dead loads, operating loads, wind forces, thermal effects, blast impacts, and seismic events outlined in the Structural Design Basis. The aim is to prevent any failure and keep deflection within acceptable limits throughout the intended lifespan of the structure. Additionally, achieving maximum cost-efficiency while utilizing selected steel materials is a key objective in this process.
By carefully choosing the stress ratio for margin calculation, keeping it below 1 but usually between 0. 7 and 0. 9, you can effectively establish a safety margin against maximum deflection. Opting for a maximum stress ratio of 0. 9 can help minimize member sizes while ensuring accuracy of input data, such as equipment weight estimates mentioned earlier.
Once the structure has been carefully planned and designed, it is time to seamlessly integrate it into the steel structure detailing software. This entails replacing the preliminary model with the finalized design, incorporating all important elements such as member sizes, positions of bracings, and more. This meticulous process ensures accuracy and precision in capturing every detail of your steel structure project.
After being generated in the structural steel detailing software, the structure is seamlessly transferred to the Plant 3D model. This streamlined process ensures accurate integration between the two systems, increasing efficiency and precision in your project.
In the Plant 3D Model, the initial structure is removed and then reviewed by the layout discipline. They carefully examine the imported structure to ensure its suitability. For example, they might identify that a bracing is obstructing an access point and request Civil to either delete or relocate it. This thorough assessment helps ensure an efficient and obstruction-free design.
-
Material take-off
Extracting the list of materials needed for a steel structure, including profiles, plates, and bolts, is now made easy with the help of steel structure detailing software. This powerful tool not only helps determine the weight of materials but also assists in calculating supply and installation costs. Moreover, it enables seamless procurement by ensuring that purchases are made on time in alignment with the project schedule and lead time requirements.
In the initial phase of design, our primary focus is on the main structure, such as columns, connecting beams, and bracings. These elements are crucial for ensuring stability in the overall structure. We prioritize working with materials that have longer lead times to ensure their availability later on. In the second phase of design, we shift our attention to smaller sections like secondary and tertiary components. These sections are more readily available in the market, making it easier for us to source them efficiently.
The successful completion of the primary structure design in the first phase not only signifies progress but also provides important input data for the foundation design. This allows us to conduct a thorough analysis and ensure that appropriate foundations can be installed. In case any adjustments are necessary, we can make changes to the structure design accordingly to ensure a seamless construction process.
PHASE 2 – DESIGN OF SECONDARY AND TERTIARY STRUCTURE
In phase 2, all the remaining structural elements, called secondary and tertiary structure, must be designed. These elements are:
- Structural members which are not necessary to provide stability of the structure: supports of all types of items: Equipment, piping, Electrical and Instrumentation items, such as cable trays, handling devices, etc.
- Walkways, access platforms, stairs, ladders, floor beams, grating, plating,
- Input data
The input data is only available progressively as the design develops, i.e.,
- Once you have obtained the equipment support details from vendors, you can rest assured that any issues or concerns with your equipment will be promptly addressed and resolved. This level of support ensures maximum uptime and productivity for your business, allowing you to stay ahead of the competition.
- Once piping Once the necessary calculations for piping routing, stress analysis, and load identification on supports have been conducted, the precise location, type, and loads required for efficient piping support can be determined and stress calculation, for the lines that require such calculations, have been performed to identify the location, type and loads on piping supports
- Once you have determined the placement of your Electrical and Instrumentation items such as panels and junction boxes, as well as planned out the routes for cable trays, you are setting yourself up for a well-organized and efficient workspace. By establishing these foundational elements, you can ensure smooth operations and prevent any potential issues down the line.
- Once we have established the layouts for handling devices and gathered all necessary vendor data, we can proceed with confidence. This approach ensures a smooth and efficient process, allowing us to make informed decisions based on accurate information. By diligently considering these factors, we can streamline our operations and achieve exceptional results.
- Once the access and escape routes have been clearly identified, it becomes crucial to address the corresponding requirements for platforms, ladders, staircases, and other necessary elements. These essential components ensure a safe and efficient means of movement within the space while adhering to regulations and promoting workplace safety. By investing in well-designed access systems, you can create a more productive environment while prioritizing the well-being of your employees.
When it comes to column access platforms, one challenge is that the input data often arrives quite late in the process. By this point, piping routing has already been completed and information on internals from the sub-vendor has been obtained to ensure proper alignment of nozzles.
The design of both the secondary and tertiary structure is a progressive process. It unfolds gradually, ensuring that all the necessary information is properly incorporated at each step. This strategic approach allows for a more thoughtful and comprehensive outcome in structural design.
When it comes to designing process plant steel structures, including process structures and pipe racks, there are several important considerations to keep in mind. These structures play a crucial role in supporting the various equipment, pipelines, and utilities required for the efficient operation of the process plant.
First and foremost, the design of process plant steel structures should prioritize safety and compliance with relevant codes and standards. It is essential to ensure that the structures can withstand the loads they will be subjected to, including dead loads (the weight of the structure itself), live loads (such as equipment and personnel), and environmental loads (such as wind and seismic forces). Accurate load calculations, based on the specific requirements of the plant, must be carried out to determine the appropriate size and strength of the steel members.
Additionally, the design should consider the layout and functionality of the process plant. The steel structure should be designed to accommodate the equipment and pipelines, allowing for proper clearance, access, and maintenance. It is essential to consider factors such as pipe routing, equipment spacing, and operational requirements when determining the layout of the structure.
Efficiency and constructability are also key considerations in the design process. The steel structure should be designed in a way that optimizes material usage, reduces fabrication and erection time, and minimizes costs. This can be achieved through the use of modular design techniques, standardization of components, and the integration of advanced detailing and fabrication technologies.
Collaboration and coordination with other disciplines, such as process engineering, piping engineering, and electrical engineering, are crucial to ensure seamless integration of the steel structure with the overall plant design. Effective communication and coordination among all project stakeholders can help identify and resolve any clashes or conflicts between different elements of the plant design, ensuring a smooth construction process.
Lastly, sustainability and environmental considerations should be taken into account. The use of environmentally-friendly materials, efficient energy consumption, and the incorporation of sustainable design principles can help minimize the environmental impact of the process plant steel structures.
In conclusion, the design of process plant steel structures, including process structures and pipe racks, requires careful consideration of safety, compliance, functionality, efficiency, collaboration, and sustainability. By addressing these factors in the design process, you can ensure the successful construction and operation of a process plant that meets the specific needs of your project.
3 thoughts on “The Impact of Structural Design on Maintenance and Longevity of Process Plant Steel Structures”